FRIEDBERG, Germany, Feb 5, 2024 – In an initial proof of concept, voxeljet AG and Parastruct GmbH have successfully tested the 3D printing of recyclable residual materials from the construction industry. For this purpose, voxeljet’s Binder Jetting 3D printing technology was used. The material tested was the Ecomould material set from Parastruct GmbH. A material set consisting of biogenic production residues from the construction industry and a mineral binder, which was developed by the Austrian start-up. Using binder jetting, Ecomould can be used to produce molded parts that are suitable for the cold casting of concrete and ceramics for interior design objects or for laminating processes. The Ecomould material was tested on a VX200 from voxeljet – a 3D printing system specially developed for research and development purposes.
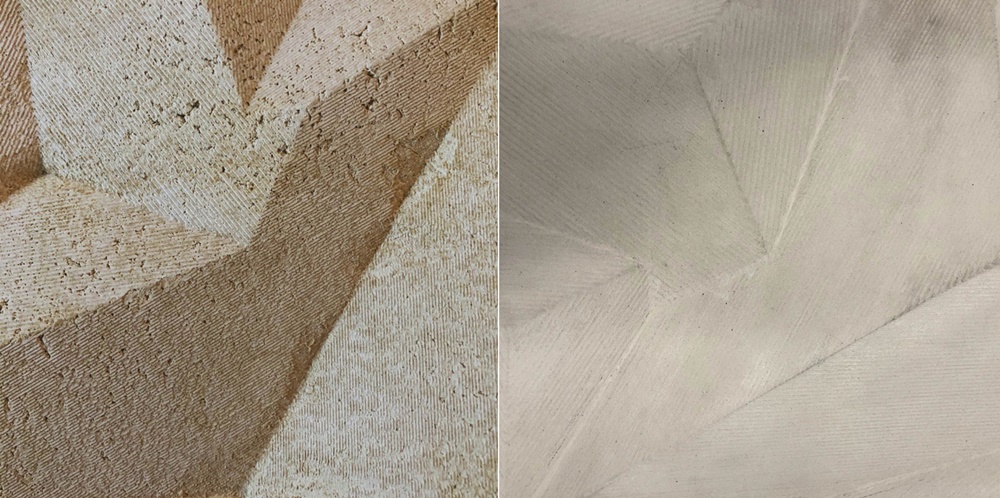
Parastruct GmbH is an Austrian company that offers a sustainable solution for recyclable mold making using their developed technology and Ecomould material set. The market for excess material recycling is expected to grow at an annual rate of 7-9% until 2025. Increasing legal obligations and customer requirements as part of Corporate Social Responsibility (CSR) strategies are driving interest and demand for sustainable value-added solutions. Parastruct utilizes 3D printing to reintroduce unused mineral materials, such as production waste from the construction industry, and biogenic resources, such as wood flour or sawdust, back into the value creation process.
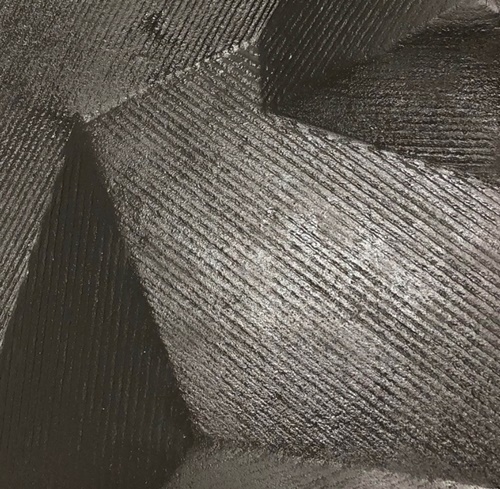
Companies can make potential savings by eliminating disposal costs, which can be as high as €75-100/t for construction waste and €70-180/t for wood, and by reducing resource expenditures to optimize overall profitability. Ecomould can assist in achieving sustainability goals, particularly in light of stricter guidelines like the EU Green Deal. Ecomould has a significantly lower CO² footprint than conventionally manufactured sand-phenolic resin molds, emitting -108.3 kg CO² per 1m² of mold surface*.
Ecomould-produced molds can be shredded and reused as particle material in 3D printing. A plastic coating can be applied as a finish, which is removable at the end of its service life. This second use of Ecomould material reduces the carbon footprint even further.
voxeljet’s binder jetting 3D printing technology is ideal for processing Ecomould due to the fact that voxeljet 3D printers are open-source systems whose printing parameters can be flexibly adapted to different material sets. Additionally, voxeljet offers a wide range of printers, currently in sizes up to 4 x 2 x 1 m, which promises easy scaling of the Ecomould results to larger, more productive 3D printers.
Interested parties are being sought to jointly advance the transformation of a more sustainable construction industry in a possible funding project.
About voxeljet
voxeljet’s (NASDAQ: VJET) roots reach back to the year 1995 with the first successful dosing of UV-resins. In the context of a “hidden” project, initial 3D-printing tests are performed at the Technical University Munich. Our company was founded on May 5, 1999 as a spin-off from TUM in Munich with a clear vision in mind: to establish a new manufacturing standard by developing new generative processes for the series-production of complex components using 3D printing. In the beginning, operations are launched with four employees at the TUM. Today, we are a globally acting, leading provider of high-speed, large-format 3D printers and on-demand 3D printed parts to industrial and commercial customers. Components manufactured with the help of our technology are flying in space, make mobility more efficient and the production of new engineering solutions possible. Visit our website www.voxeljet.com, and follow us on Linkedin, or on Twitter.